The process of brazing entails the joining of metals with melted aluminum. It produces a much cleaner joint than other joining methods such as welding and eliminates the need for post-processing.
Aluminum brazing is ideal for large flat surface materials, as it uses pressure to reinforce joints. Since it can be used to join parts made of different materials, it is also a cost-effective option for composite or assembled parts.
Because brazing is performed in large furnaces that can accommodate bulk materials, it is particularly well-suited to mass production. If necessary, another brazing material can also be used in the process.
There are two types of aluminum brazing: aluminum dip brazing and aluminum vacuum brazing. Each process offers a distinct set of advantages.
Aluminum Dip Brazing
Aluminum dip brazing involves placing brazing sheets in molten salt to break down metal oxides. The filler metal is initially positioned outside of the joint and heated to molten temperature before it enters it. As it travels through the joint, the filler metal expels the flux from it.
Unlike aluminum vacuum brazing, this procedure does not apply pressure to a joint. As a result, it can be used on parts without large flat surfaces or similarly sensitive materials.
Alloys subjected to aluminum dip brazing offer greater strength and an increased resistance to corrosion. Since they conduct heat effectively, they are also particularly useful for heat transfer applications.
Aluminum Vacuum Brazing
Aluminum vacuum brazing uses a clean vacuum environment without a flux. Because it applies pressure to the parts to be joined, it can only be used for flat, horizontal surfaces. In contrast, this process is designed for parts that are not flat.
During aluminum vacuum brazing, pressure is applied to a metal part to break down its oxide layer. The filler metal is then diffused into the base metal. Because the filler metal is inserted into the joint before brazing begins, the process results in a cleaner and more precise joint.
Aluminum vacuum brazing can be performed on metals with objects and cross-sections with different dimensions, making it a particularly versatile solution. Because it offers greater precision than dip brazing, it’s best suited to any application that requires strict consistency.
Lynch’s Brazing Solutions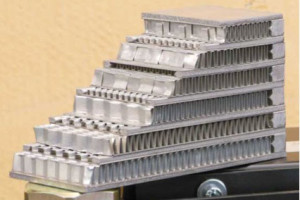
Aluminum dip brazing and aluminum vacuum brazing are far better options than other joining methods, providing manufacturers with more durable and effective products. As with any manufacturing technique, however, any prospective user should thoroughly consider their needs to ensure that they invest in the best strategy for their applications.
If you need appropriate equipment for your brazing processes, the experts at Lynch Metal can help. Since 1991, we’ve been a trusted leader in the distribution of flux brazing alloys used in aluminum dip brazing and aluminum brazing fins and sheets used in aluminum vacuum brazing.
Our extensive inventory, specialized processing equipment, and years of experience make us the go-to resource for your aluminum brazing needs. From aerospace to telecommunications, we’re able to provide manufacturers in every major industry with reliable and efficient solutions to their brazing challenges.
For more information on our products and services, contact us today. If you’re interested in working with us, request a quote on our website.